Quality and Safety
Quality and Safety-Related Targets
Meiji Group 2026 Medium-Term Management Plan
- Data target range or company leading initiatives
- 1: Meiji Co., Ltd. (consolidated)
- 2: Meiji Seika Pharma Co., Ltd. (unconsolidated)
Major initiatives | Metrics | Results / progress | Targets | |
---|---|---|---|---|
FYE March 2025 | FYE March 2027 | |||
1 | Strengthen quality initiatives by promoting Meiji Quality Comm activities based on Meiji's Global Quality Policy | Number of serious quality accidents | 1 case | 0 cases |
Acquisition rate of GFSI recognized standards at all locations of partner companies (product outsourcing/suppliers) |
94.2% | 100% | ||
Plant audit rate for suppliers of important managed raw material | 80.9% | 100% | ||
2 |
|
Number of serious nonconformities such as recalls in manufactured and sold items | 0 cases | 0 cases |
Number of serious indications in responses to regulatory authorities | 0 cases | 0 cases |
Food Safety and Quality Assurance
Initiatives to Enhance Quality
Quality Policy
Meiji Co., Ltd. has established its own quality management system, Meiji Quality Communication ("Meiji Quality Comm"). This system is founded in the Meiji Group's System of Principles, and we are strengthening our quality initiatives on a daily basis.
Meiji Quality Comm has issued a Quality Policy, which provides Meiji's principles and guidelines as they pertain to quality management.
Meiji's Quality Policy
At Meiji, we pursue “Tastiness and Enjoyment” and strive to meet the expectations of our global customers for wellness, safety, and reassurance. As “Food and Health” professionals, every employee at Meiji works to fulfill the following duties.
- Engaging in quality assurance activities within all organizations, including development and design, sourcing, production, logistics, sales and communication.
- Providing customers with accurate information, sincerely listening to customer feedback and applying those opinions towards improving our products and services.
- Acting based on a constant awareness of legal compliance and the commitment to providing safe products.
Quality Management System
Our Quality Assurance Regulations, founded in our Quality Policy, clearly stipulate important items with regard to safeguarding quality in a range of duties for our functional divisions, from development and design, to sourcing, to production, to logistics, to sales and communication. In addition, our Quality Assurance Standards provide detailed specific duties, procedures and criteria. Through these, we continue tomake improvements via the management cycle in all functional areas, from development and design to sales and communication, in order to gain the trust and satisfaction of our customers. Our top management also reviews these activities in assessment of our quality activities.
Meiji Quality Comm serves as Meiji Co., Ltd.'s shared posture in pursuit of customer satisfaction.
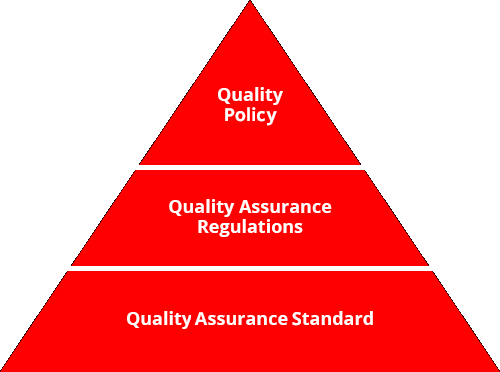
Quality Management Structure
We promote quality activities centered on the Meiji Quality Communication Review, a biannual meeting chaired Chief Operating Officer of the Food Segment. At this meeting, we check the progress of our quality-related initiatives and discuss measures to resolve any issues that may be present. In addition, we have established the Meiji Quality Communication Liaison Committee, headed by the Vice President, Quality Management Div., to plan and promote Meiji Quality Communication Advancement Activities.
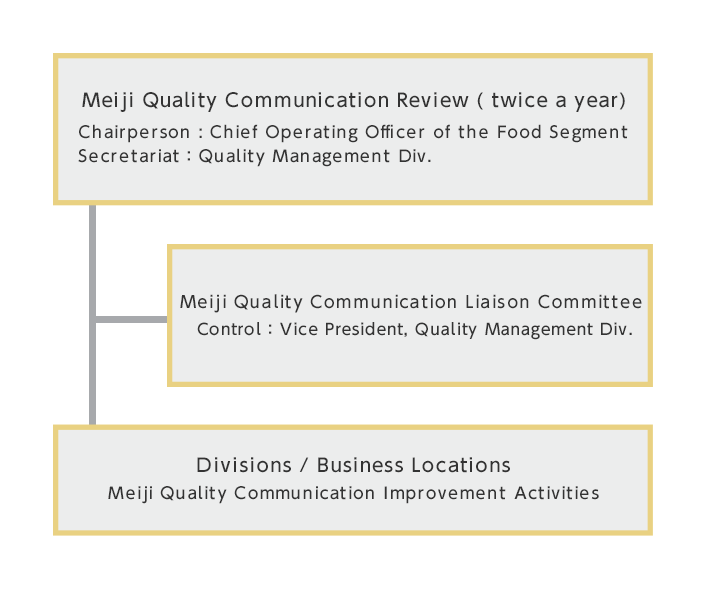
Initiatives via the Value Chain
Meiji Quality Comm: Overview by Process
- Development and Design Functions
Our Meiji Quality Comm quality management system is engaged in various processes beginning in the product development stage. This system asks, how can we create products offering value to our customers? To answer that question, we are diligently conducting a series of studies into markets and their consumers, meanwhile consistently advancing research and development founded in our accumulated expertise. Crafting a concept for our product becomes a key driver affecting all downstream functions, such as manufacturing and distribution. - Sourcing Function
When selecting raw materials, safety and consistency are key. While safety is a naturally essential element, even a good raw material must be consistent in its availability in order for us to also be consistent in manufacturing the resulting products. Therefore, we must ensure that we can consistently secure raw materials meeting the applicable standards. In order to achieve this, trust and communication with suppliers is extremely important. - Production Function
Within the various production processes ongoing in our plants, we have established a system to ensure safety and to build quality into our products. In order to enable production with consistent product quality versus initial designs, we provide a detailed set of instructions for each product, such as raw material mixing, process conditions, and check points. In addition, we carry out inspections and monitoring at each process step, from receipt of raw materials to mixing and filling, and a control system is in place to verify that production follows the process conditions laid out in the initial design. - Logistics Function
Our logistic teams are tasked with delivering finished products from our plants to distribution centers used by dealers, wholesalers, and mass retailers. When practicing quality control, there are five key words: The five key words in practicing quality control are "product," "quantity," "freshness," "time," and "behavior." These are the "Five Promises," areas of key attention we have established to satisfy our customers and ensure that they can enjoy our products' deliciousness. We provide quality assurance through each and every one of us maintaining a keen awareness of these promises. - Sales and Communication Functions
The major role of these functions is to provide a clear, accurate picture of the value of our products to the customer in a way that shares the consumer viewpoint, as well as to share that value with them. The mission for these functions is to communicate the high quality that we have built up through the functions from development and design, to sourcing, to production, to logistics. These teams are the final runner in our quality relay race, helping customers select our products knowing their value.
Food Safety Efforts
As part of our food safety efforts, we have introduced HACCP at all of our plants. In addition, in FYE March 2021, we achieved 100% acquisition worldwide of standards recognized by GFSI, a global food safety management organization.
Obtaining Anti-doping Certification for Sports Nutrition Products
The Meiji Group has obtained Informed Choice certification, a global anti-doping certification program, for the majority of our sports nutrition products. Based on the program, through analysis using advanced technologies and manufacturing process audits, products are checked to ensure they are not contaminated with any banned substances. We will continue providing certified products for athletes so that they can consume without concern as they strive to achieve their goals, and also for sports lovers.
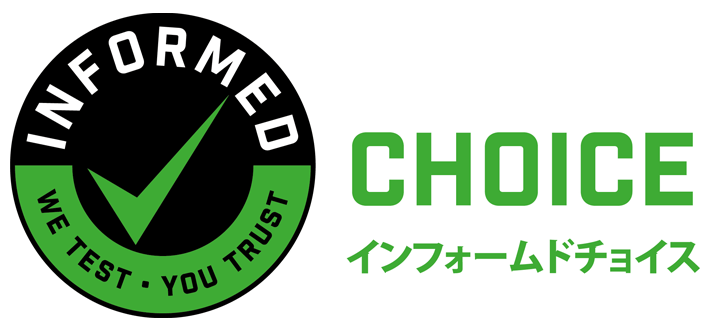
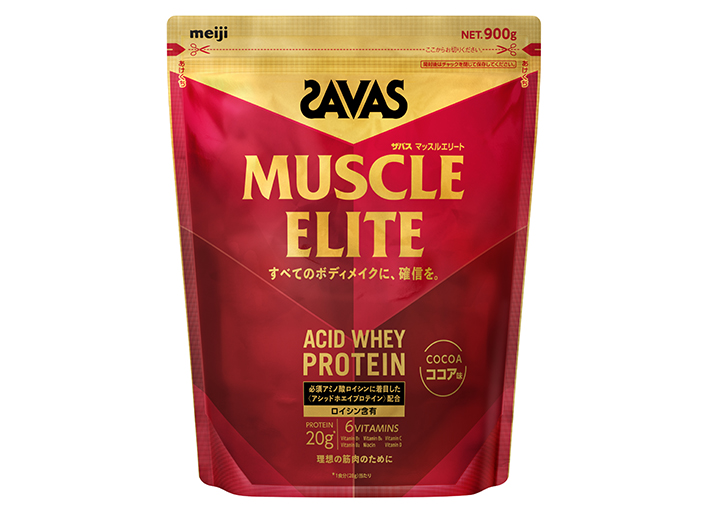
SAVAS Muscle Elite, with Informed Choice certification
Genetically Modified Ingredients
The Meiji Group makes appropriate decisions regarding the use and labeling of genetically modified ingredients in its products in accordance with the laws and regulations of each country concerning the use and labeling of genetically modified ingredients in food products, and does not use any raw materials that are subject to mandatory labeling under the genetically modified labeling system.
Initiatives regarding the Use of Food Additives
The Meiji Group uses food additives whose safety has been confirmed in accordance with the standards of each country, and when using such food additives, we clarify the purpose of use and make appropriate decisions on the amount and method of use.
In addition, a Food Safety Committee with external members has been established within the company to appropriately respond to consumer interest in food safety and trends in food safety administration.
Employee Training on Quality and Labeling
To further improve the quality level and comply with the Food Labeling Act, we conduct quality and labeling related training for employees in charge of development, manufacturing, and sales.
We will continue to conduct employee training and strive to provide customers with information on product quality, safety, and security.
Unit: Persons
Educational Program Content | FYE 3/2022 | FYE 3/2023 | FYE 3/2024 | FYE 3/2025 | |
---|---|---|---|---|---|
Employee training on quality | 8,186 | 9,001 | 8,800 | 8,894 | |
Quality training for sales representatives (Calculated as the cumulative number conducted twice a year) |
2,921 | 2,921 | 2,731 | 2,800 | |
Basic lecture series on quality control for plant employees | 6,200 | 6,000 | 6,000 | 6,000 | |
Quality assurance meetings for section managers at plants | 86 | 80 | 69 | 94 | |
Employee training on the Food Labeling Act | 230 | 334 | 371 | 522 | |
Workshops for new employees | 40 | 91 | 246 | 339 | |
Periodic workshops for technical employees | 190 | 190 | 125 | 111 | |
Workshops on a particular topic | - | 53 | - | 72 |
Conduct supplier audits and training in quality control
In the food business, we regularly conduct annual audits and training of suppliers, focusing on food safety and quality control systems, based on the criteria to ensure a stable supply of raw materials and packaging materials in conformance with relevant laws and regulations and our own standards.
Unit: Cases
FYE 3/2021 | FYE 3/2022 | FYE 3/2023 | FYE 3/2024 | FYE 3/2025 | |
---|---|---|---|---|---|
Meiji | 41 | 82 | 66 | 93 | 91 |
Pharmaceutical Reliability Assurance
Quality Management Based on Reliability Assurance Systems
Reliability assurance system (Meiji Seika Pharma)
Meiji Seika Pharma has established a system for the research, development, and stable supply of world-class products, as well as a system to collect safety information and provide information on proper use. Through this reliability assurance system, we will contribute to society by earning the trust of patients and healthcare professionals.
Meiji Seika Pharma Reliability Assurance Policy
Meiji Seika Pharma has established its Meiji Seika Pharma Reliability Assurance Policy, as follows. We conduct our business with the full recognition of the meaning and the role of this policy.
Meiji Seika Pharma will make efforts to be trusted by patients and healthcare professionals and contribute to society.
In the areas of pharmaceuticals and medical devices, we conduct our business activities with the aim of contributing to society by developing useful and high-quality products; ensuring production and stable product supplies to patients and healthcare professionals and providing necessary and prompt product information to them.
To achieve this aim, we thoroughly comply with applicable regulations and standards, as well as other social or ethical requirements, and act ethically and morally as persons involved in a life-related industry.
All of us will continue to make sincere and humble efforts to offer safe use of products and information to patients and healthcare professionals.
To work together, we ask our business partners to understand the aforementioned attitude.
With this policy for business activities to assure the reliability of our products and information provided to patients and healthcare professionals, we will continue to make efforts to have their trust and contribute to society.
Reliability Assurance Guideline
Product Initiatives
Meiji Seika Pharma is taking actions to improve the reliability of its products. Here, we define "products" to include not only the products themselves (pharmaceuticals and medical devices, hereinafter collectively "pharmaceuticals, etc."), but also data obtained through development, clinical trials, and other processes, as well as information on proper use after launched. The Meiji Seika Pharma Reliability Assurance Guideline form the foundation of these actions.
Meiji Seika Pharma Reliability Assurance Guideline
With the underlying policy (Meiji Seika Pharma Reliability Assurance Policy) of "earning the trust of patients and healthcare professionals, and contributing to society," we have established the Meiji Seika Pharma Reliability Assurance Guideline and take actions to ensure the reliability of our products.
In addition, regulatory authorities have set rigorous standards for pharmaceuticals, etc., from development to manufacturing, shipment, collection of information on adverse events, and provision of information on proper use. Based on these standards, we have established in-house standards and procedures to ensure tests are executed properly and test data is accurately collected, and we are working to improve the reliability of our data and information. These guidelines are also applied to Group companies*.
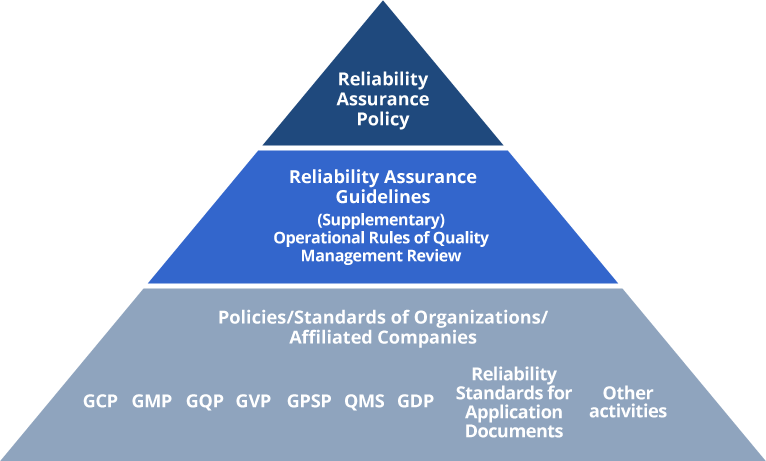
GCP: Good Clinical Practice
GMP: Good Manufacturing Practice
GQP: Good Quality Practice
GVP: Good Vigilance Practice
GPSP: Good Post-marketing Study Practice
QMS: Quality Management System
GDP: Good Distribution Practice
Plan-Do-Check-Act (PDCA) Cycle
Based on these guidelines, the Reliability & Quality Assurance Division serves to investigate and provide guidance to all Group companies regarding their compliance status with laws, regulations, and various standards concerning of the development, production, supply and pharmacovigilance of our pharmaceuticals, thereby promoting product reliability assurance. The Reliability & Quality Assurance Division operates independently of our development, production, and sales divisions, creating a system ensuring reliability based on objective judgment. Furthermore, in order to not only ensure but also improve the reliability of our products, we have established the Operational Rules of Quality Management Review as a tool to make continuous improvements while utilizing the PDCA cycle.
In order to improve the reliability of our products, the Operational Rules of Quality Management Review stipulate that each division shall set its own quality policies and targets to achieve, and that the management team shall be the core driver in periodically reviewing how well these targets have been achieved continuously improving quality through the PDCA cycle.
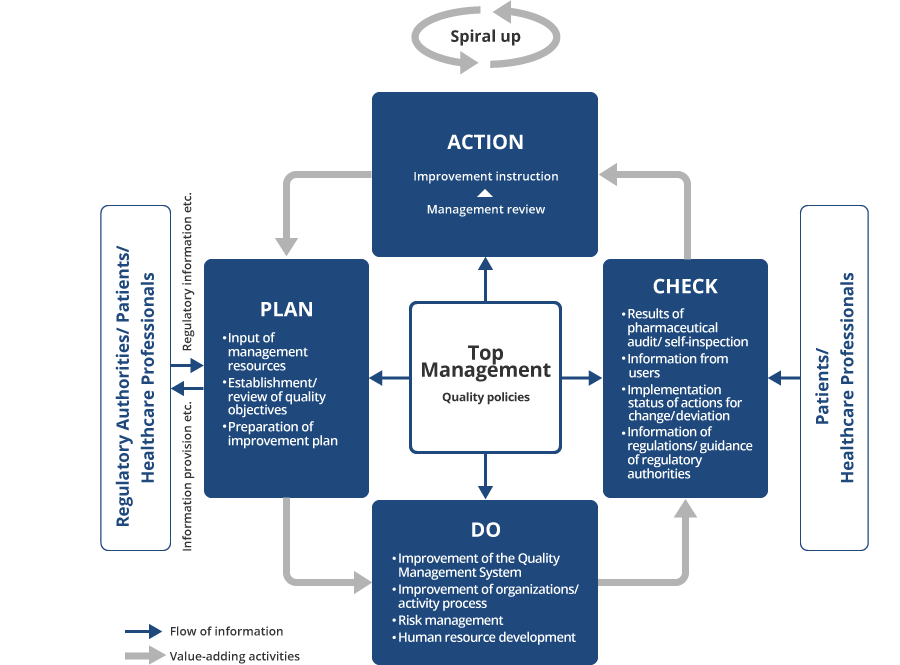
Quality Assurance System
As well as complying with Good Manufacturing Practice (GMP) in Japan, Europe, and the United States, Meiji Seika Pharma has established its Quality assurance policy, a policy for quality of products sold under the Meiji brand name and existing under the Meiji Seika Pharma Reliability Assurance Guideline. This policy is also applied to our products other than pharmaceuticals(ex, medical devices). By sharing this policy with Meiji Seika Pharma's fellow Group companies, we will reduce potential risks related to product quality at each stage of production (manufacturing control and quality control) and implement a global-standard quality system by practicing continuous quality improvement.
Furthermore, we are advancing consistent quality assurance activities based on our Quality assurance policy throughout the entire supply chain, from raw material sourcing to production, distribution and other operations. For example, in order to safeguard product quality, we conduct audits not only at our in-house plants, but also at contract manufacturers and raw material suppliers in Japan and overseas, and provide risk reduction guidance on a regular basis.
In addition, when shipping pharmaceuticals to the market, our quality assurance managers check all manufacturing records in accordance with the law before approving their shipment. This system is in place so that we can deliver pharmaceuticals that patients and healthcare professionals can use with peace of mind.
Safety Management System
Meiji Seika Pharma strives to minimize safety risks by collecting safety information (e.g., information on adverse events) from Japan and overseas related to the pharmaceuticals, medical devices delivered to customers, objectively evaluating and reviewing this information, and promptly providing the information necessary for the proper use of its products.
In addition, we are working to improve the safety and reliability of our products by providing information on post-marketing use results surveys to medical professionals.
Quality Improvement and Personnel Development
We foster the ability of our employees to improve operations proactively. We hold meetings to share and discuss the achievements of quality improvement activities and engage in other activities to develop our personnel.
Response to Quality-Related Incidents
If a quality-related incident occurs, our head office collects quality information from plants, affiliated companies, and the respective divisions involved. This information is summarized and shared with senior management. We take any necessary measures and implement preventive measures as promptly as possible.
Concerning Response to Business Improvement Order
During the process of the investigation of the Kobayashi Kako itraconazole contamination incident that occurred in December 2020, it was discovered that the stability test data used in the registration application for rosuvastatin tablets, which were developed jointly with Kobayashi Kako and registered by Meiji Seika Pharma, had been modified.
As a result, a Business Improvement Order was issued by the Ministry of Health, Labour, and Welfare (MHLW) in May 2021. In response, we issued a business improvement plan in June 2021.
Subsequently, in accordance with the business improvement plan, we created a business procedure manual for joint development partners, conducted education and training to ensure comprehension of those procedures, improved the details of joint development agreements, and reinforced reliability audits for registration application materials. We take this Business Improvement Order extremely seriously and will work to restore our credibility.
Quality Assurance Training for Employees
Meiji Seika Pharma provides ongoing quality and safety-related education, including GVP, GMP and QMS, to all employees. Since the revision of the Pharmaceutical Affairs Law in August 2021, we have been providing training (including GVP, GMP, and QMS) to ensure compliance with laws and regulations related to pharmaceutical affairs.
<FYE 3/2025 Training Activities>
- Training (e-learning) for all employees to ensure compliance with pharmaceutical laws and regulations: Conducted 8 times a year, number of attendees 2,100 (100% attendance rate)
KM Biologics holds lectures on GMP compliance annually for all employees, and holds training regarding our pharmaceutical quality management system. Our aim is to help each and every employee realize that paying close attention to how to best manage quality at each worksite leads to quality improvements overall.
<FYE 3/2025 Training Activities>
- GMP compliance training for all employees: held annually, number of attendees: approximately 2,000
- Quality training (e-learning) for all employees: held annually, number of attendees: approximately 2,000 (100% attendance rate)
Supplier Audits
In the pharmaceutical business, we check that suppliers have effective quality systems in place based on GQP and GMP, the status of their manufacturing and quality controls, the status of their facilities and equipment management, and the status of their employee education.
Unit: Cases
FYE 3/2021 | FYE 3/2022 | FYE 3/2023 | FYE 3/2024 | FYE 3/2025 | |
---|---|---|---|---|---|
Meiji Seika Pharma | 184 | 126 | 142 | 153 | 165 |
KM Biologics | 25 | 21 | 31 | 73 | 69 |